Force Control with Series-Elastic Actuators
WPI, Project for Robot Sensing: March-May, 2014
A class project for "Unified Robotics: Sensing". The task: apply precise amounts of force to an actuator, and use this to erase a whiteboard while hanging from a tether
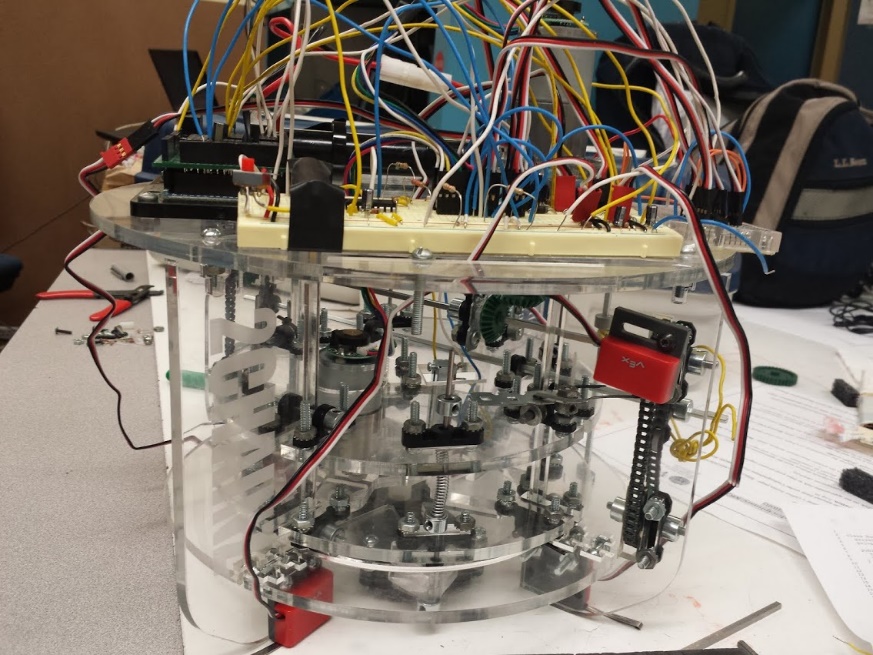
The robot was built almost entirely out of laser-cut acrylic pieces, and engraved with its nickname "2-CHAINZ" in honor of the two chain-and-sprocket mechanisms that powered the actuator. Force control was done using a typical linear series-elastic setup: two acrylic plates slid on four connecting rails, with springs sandwiched between them. A linear potentiometer connected to both parts provided the distance between them, allowing us to calculate and control the applied force. The motor driving the back plate was controlled with a PID loop that maintained the actuator at a constant pressure.
To actually erase, we made the eraser actuator spin using a "multiple gearing" mechanism, which uses grooves, sliding pins, and an axle-less gear to accomplish essentially the same thing as an ordinary gear pair. Why? It was fun to design and build. As far as we could tell, there is no good reason to ever use this mechanism in any application.